Counter-Current Scrubber
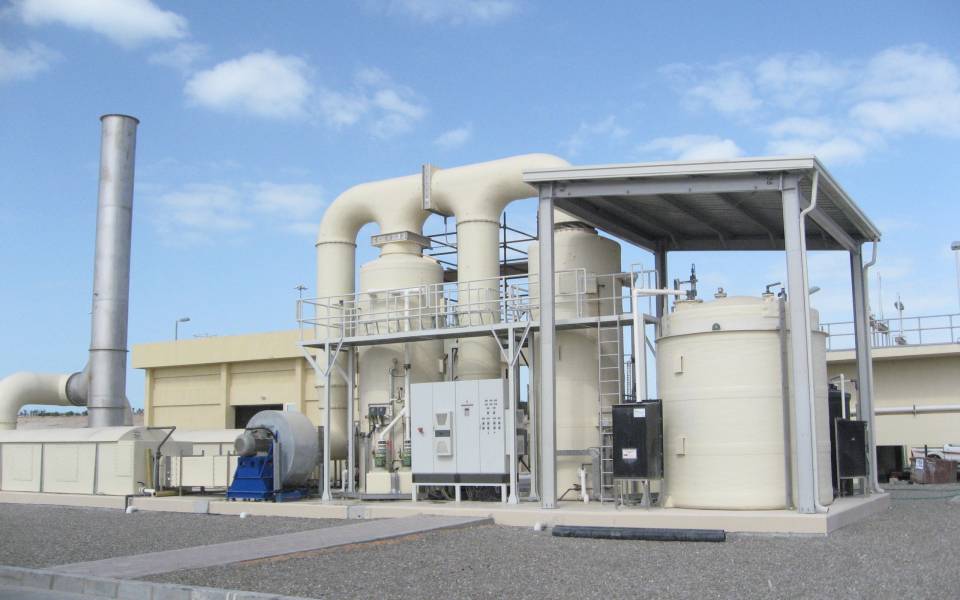
Counter-Current Scrubber
Ideal against
pollutants from the exhaust air
When it comes to exhaust air purification, compounds that are particularly harmful to the environment and health pose a major challenge and must be purified to very low clean gas values. Our counter-current scrubber offers a cost-effective and efficient solution here.
Choose our innovative and reliable solutions for a clean environment and a healthy future.
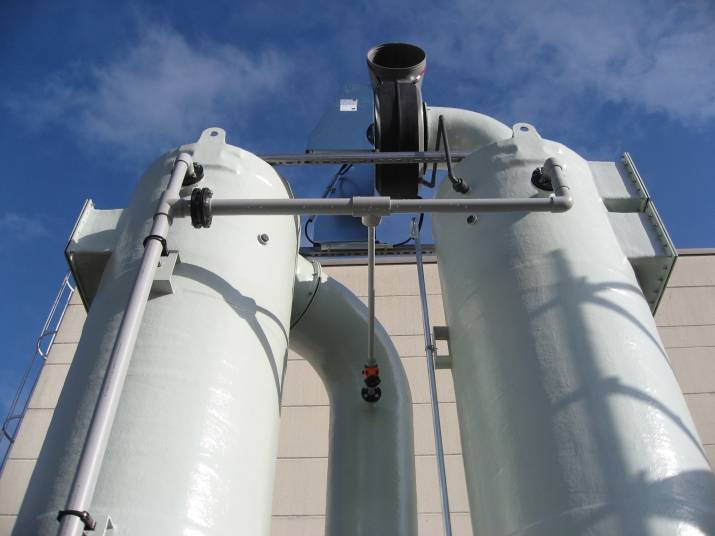
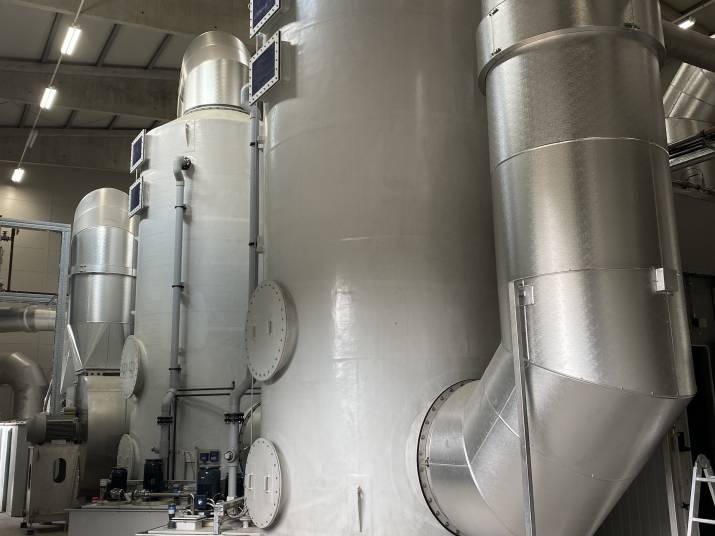
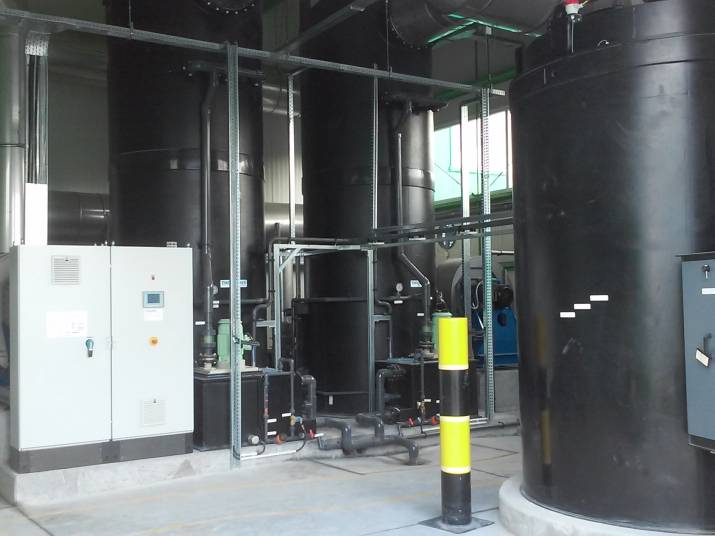
Benefit from our
counter-current scrubber
- Low space requirement
- Separation efficiency > 99% with heavily polluted exhaust air
- Low pressure loss due to high-performance packing
- Maintenance-friendly front panel
- Demand-oriented dosing of chemicals
- Optimized energy consumption
- Level control in the washer sump
- Dry run protection
- Monitoring of the nozzle pressure
- Fully automatic, measured value-controlled regulation of chemical dosing
- Automatic desalting
- Frost protection for outdoor installation
- Low pressure loss
- Low risk of clogging due to the choice of the right packing
- System components made of corrosion and chemical-resistant plastics
- Optimized for fluctuating raw gas loads
- No adaptation phase
- Active references of all sizes
- Worldwide delivery
Conception
Wet separation
Single-substance problems in exhaust air purification very often involve compounds that are particularly harmful to the environment and health and must be purified to very low clean gas values. A particularly cost-effective concept for this task is the counter-current scrubber.
The functional principle of a countercurrent scrubber is wet separation. Air pollutants and odorous substances flow in countercurrent through a packed column sprinkled with liquid. The exhaust air comes into contact with the scrubbing liquid. The pollutants and solid particles are removed by physical or chemical absorption, oxidation or condensation. The pollutants accumulate in the aqueous phase and are finally discharged. Depending on the degree of contamination, chemicals such as oxidizing agents, acids or alkalis can be added to the scrubbing water to increase the degree of separation.
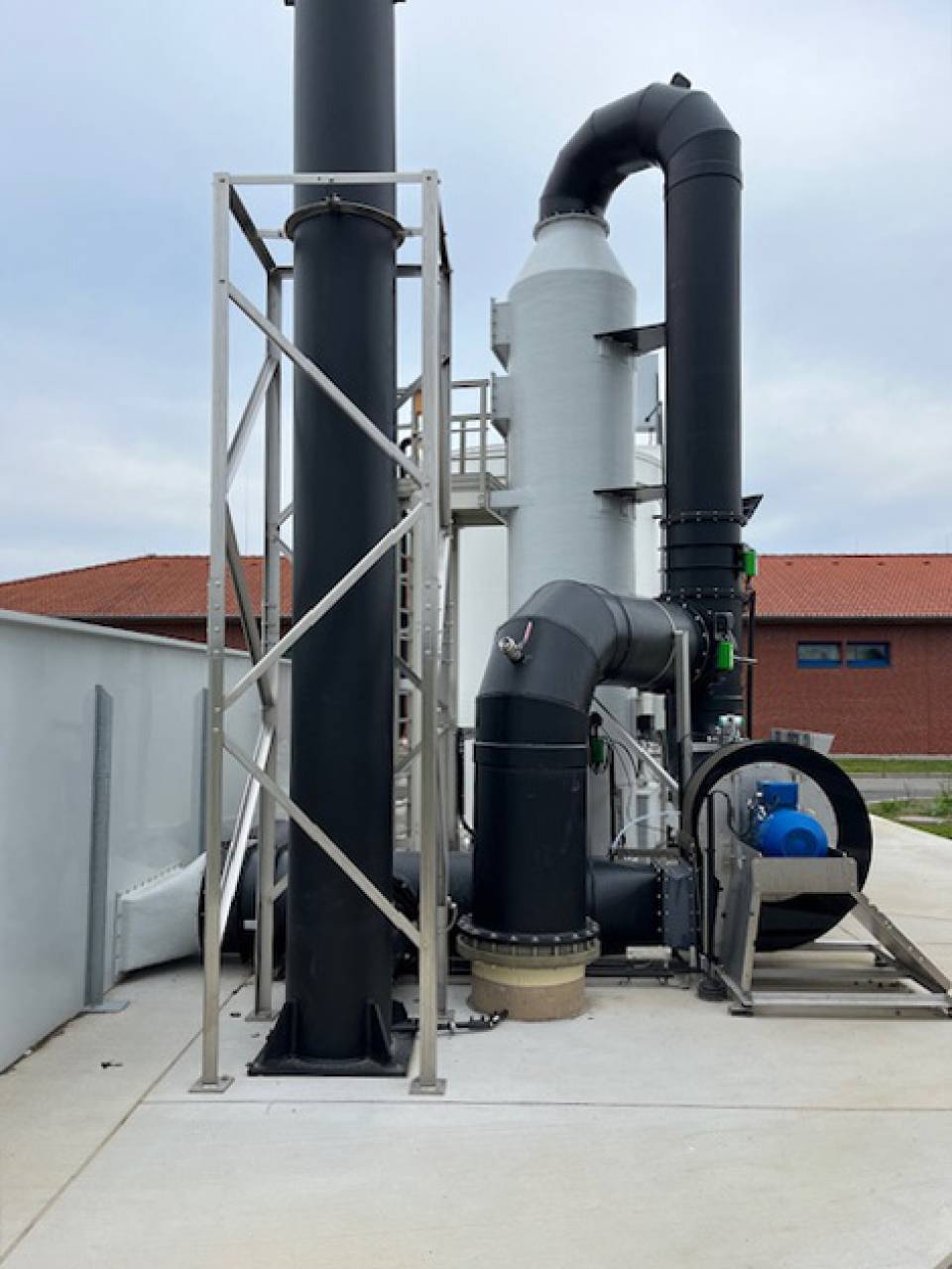
Applications
Typical applications are the separation of inorganic and organic acids (HCl, HF, SO2, NOx, acetic acid) as well as H2S, ammonia and water-soluble organic compounds (acetone, alcohols, etc.).
- Microelectronics
- Chemical industry
- Metal processing
- Food industry
- Feed production
- Composting (waste treatment plant)
- Sewage treatment plants
- Mechanical-biological waste treatment plants (MBT)
- Pharmaceutical industry
- Sewage sludge drying
- Carcass disposal
- Automotive industry
- Biogas plants
- Brewery
Projects implemented worldwide
with a Counter-current Scrubber
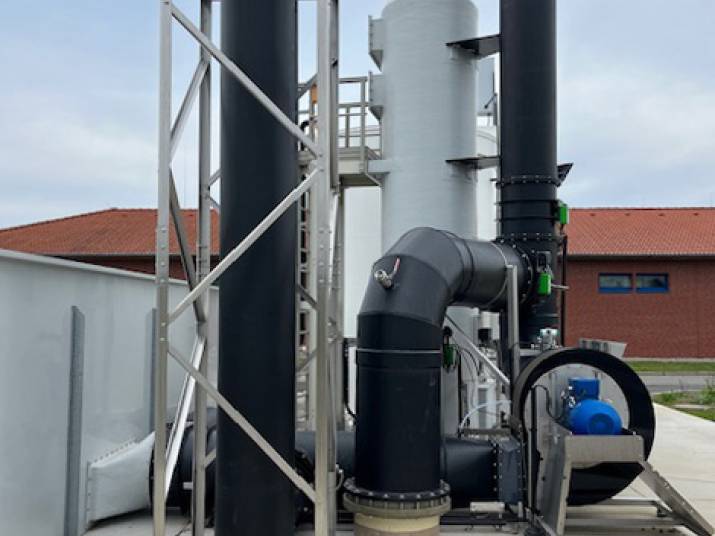
Stavenhagen sewage treatment plant / Germany
At the Stavenhagen sewage treatment plant, the exhaust air (10,500 m³/h) from various encapsulated structures with high odor emissions from mechanical, biological and anaerobic wastewater treatment as well as storage tanks for sludge and substrates is treated with a two-stage exhaust air cleaning system. The exhaust air is cleaned in an alkaline/oxidizing countercurrent washer to minimize the load from acidic pollutants (e.g. H2S). The exhaust air is then treated in a biofilter. This further reduces the pollutants and reduces the odor.
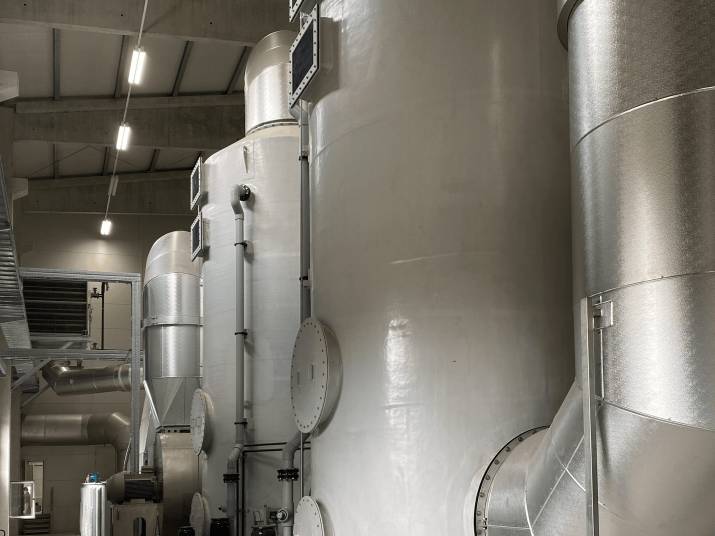
Sewage sludge drying Altenstadt / Germany
The process air (50,000 m³/h) from a sewage sludge dryer is cleaned. To treat this exhaust air, the exhaust air is first treated in an acidic washer to separate the ammonia. The second washer is set to alkaline-oxidizing by adding caustic soda and hydrogen peroxide to remove H2S and other acidic components. The exhaust air must then be heated to reduce the relative humidity to approx. 60%, and then freed of other organic odor carriers in an activated carbon filter.
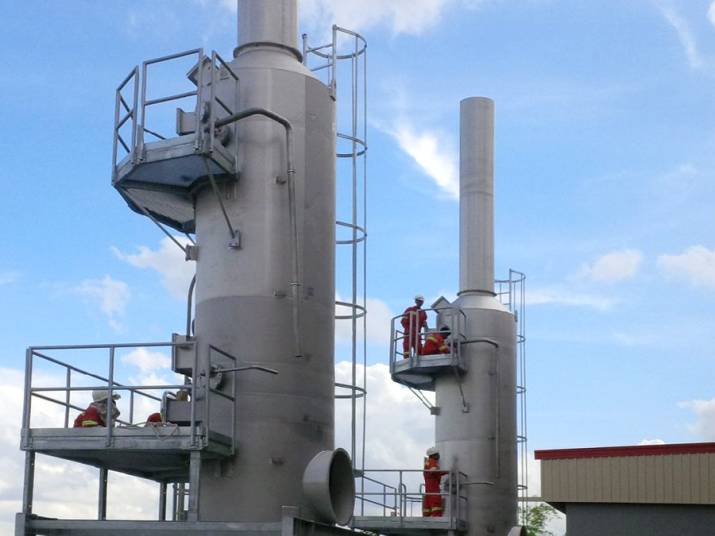
Brewery in Phnom Penh / Cambodia
In a brewery in Cambodia, the dust and SO2-laden flue gases from four steam boilers are cleaned. To do this, the flue gas from two steam boilers is combined and cleaned in a countercurrent scrubber each with a capacity of 26,000 m³/h.
FAQ about the Counter-Current Scrubber
Normally, the filling material do not need to be replaced and have a life expectancy of > 10 years. Should this nevertheless occur (e.g. due to deposits, calcification, overgrowth due to sludge ingress), the filling material can be removed through the maintenance opening located above the support grid. Refilling is carried out via the upper maintenance opening in the area of the nozzle block.
We give no guarantees for odour after a scrubber. If the components can be sufficiently converted into the water phase and react with the added chemicals, the scrubber is very efficient with regard to the separation efficiency of individual substances (e.g. H2S, NH3, mercaptans). However, other odour-relevant compounds may be present in the exhaust gas stream in addition to the lead components mentioned, which cannot be sufficiently separated in the scrubber.
NOx capture is significantly worse. In particular, a distinction must be made here between the individual forms of oxidation. NO2 is captured in the scrubber with 80-90%, whereas NO cannot be retained.
Depending on which substances are to be washed out, a cross-flow scrubber can be designed as a 1-stage, 2-stage or 3-stage scrubber.
A scrubber has a pressure loss of approx. 500 Pascal.