Biofilter
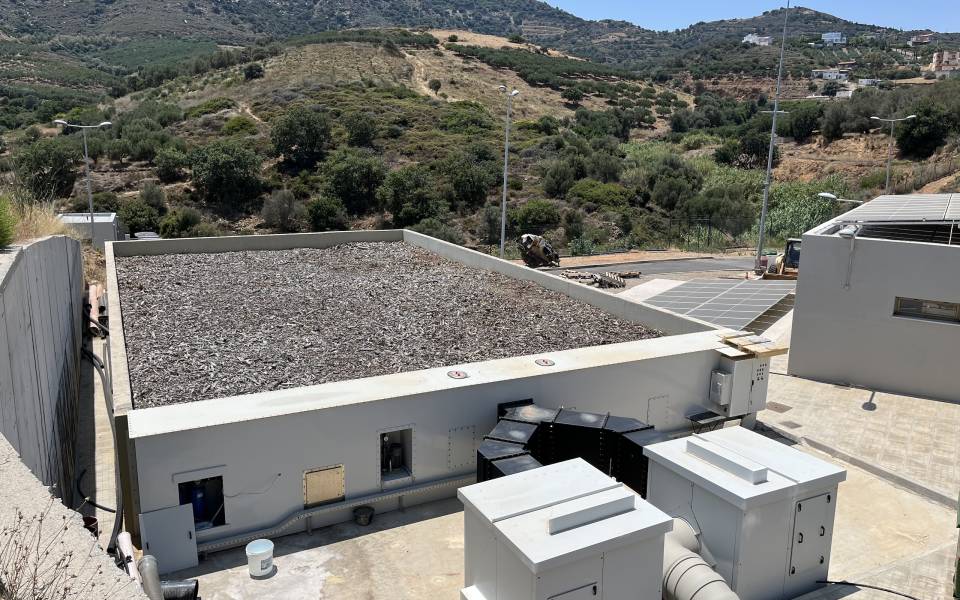
Biofilter
The cost-effective solution
Biofilters are innovative and sustainable solutions for effective odor removal in industrial and environmental applications. These advanced systems use biological processes to efficiently reduce odors and help improve air quality. Discover with us the advantages of biofilter technology for your needs in air purification and environmental protection!
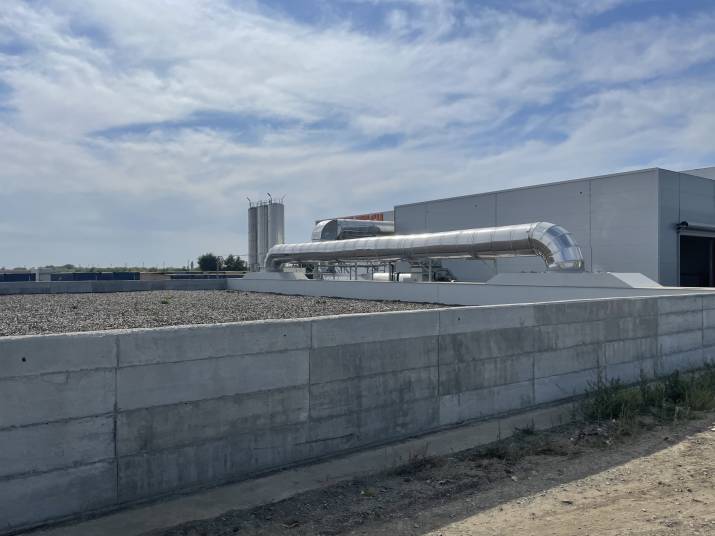
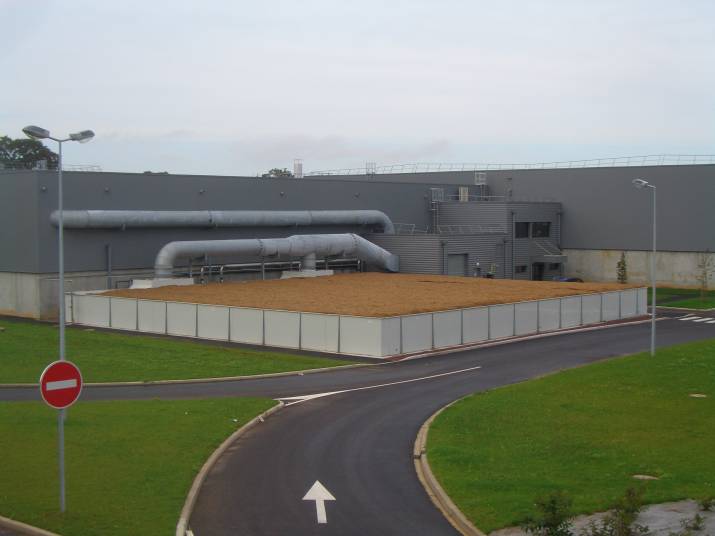
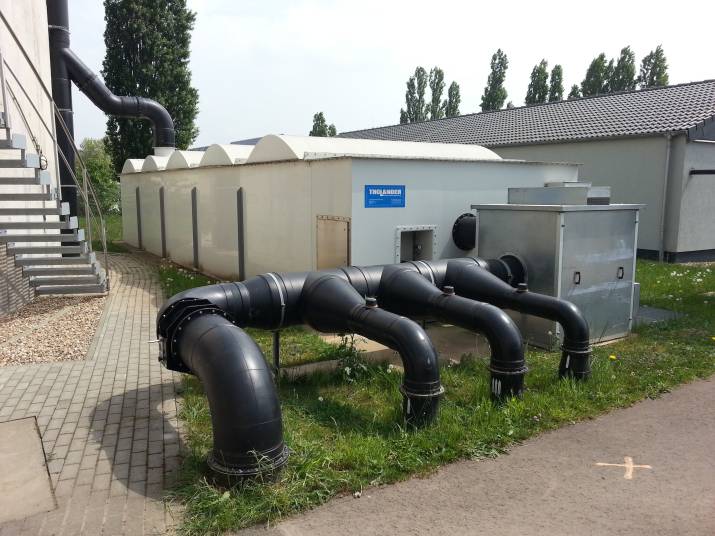
Benefit from a biofilter
- Uncomplicated process technology
- Support from the operator’s permanent staff
- Advantage of the natural reaction conditions of the material degradation
- Flexible concept
- energy requirements
- Water consumption and wastewater generation
- Use of chemicals
- Maintenance costs
- Humidification of the air to 98% RH
- Space-saving arrangement in the biofilter housing (air distribution channel)
- Dosing of various chemicals for pre-separation of e.g. NH3 or H25 possible
- System components made of corrosion- and chemical-resistant materials
- High internal surface for the settlement of microorganisms
- Uniform flow
- Good drainage effect
- Active references of all sizes
- Worldwide delivery
Conception
Biofiltration
Biofilter technology offers a cost-effective solution for eliminating odors and treating low-concentration exhaust air streams. It works under natural conditions such as ambient temperature, neutral pH and normal pressure without producing problematic end products. A biofilter consists of organic material populated with microorganisms. These break down pollutants by dissolving the exhaust air through sorption and in the moisture film. Optimal exhaust air parameters such as a temperature of 15-40 °C, high water vapor saturation and low pollutant concentrations are crucial for the efficiency and service life of the biofilter.
Applications
Biofilters are unbeatable when it comes to cleaning odorous or low-concentration exhaust air. We have over 800 reference systems in these areas. They are also suitable for exhaust air containing VOCs, where other processes would be economically or ecologically unviable.
- Food production
- Sewage treatment plant
- Compost plant
- MBA
- Leather production
- Tobacco processing
- Fermentation
- Brewery
- Waste treatment
- VOC removal
- Waste water pumping station
- Individual applications
- Sewage sludge and waste drying
- Oil mills
- Animal processing and slaughterhouses
Projects implemented worldwide
with a Biofilter
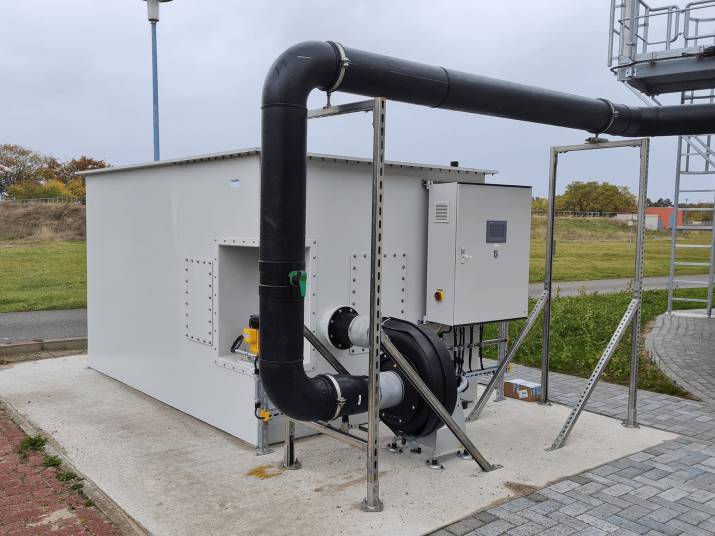
Cottbus waste water treatment plant / Germany
For the Cottbus WWTP, a biofilter was installed as a compact system for the treatment of 1,500 m³/h of exhaust air from the sludge storage tank, centrate storage, pump storage and mechanical sludge dewatering. A second biofilter cleans the exhaust air (350 m³/h) from the mixing tank. This is also designed as a compact system with an integrated pre-scrubber.
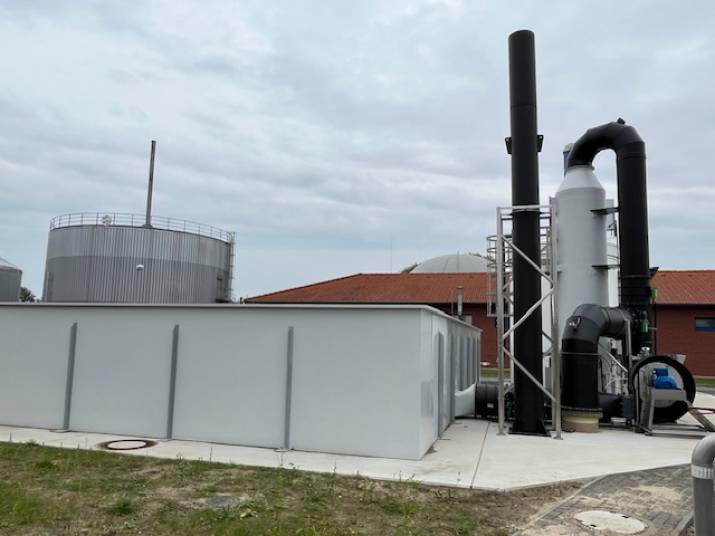
Stavenhagen waste water treatment plant / Germany
At the Stavenhagen WWTP, the exhaust air (10,500 m³/h) from various encapsulated structures is collected and cleaned. Connected are: mechanical, biological and anaerobic wastewater treatment as well as storage tanks for sludge and substrates with high odor emissions. The exhaust air is cleaned in an alkaline/oxidizing counter-current scrubber to minimize the load of acidic pollutants (e.g. H2S). The exhaust air is then treated in a biofilter. This further reduces the pollutants and reduces the odor.
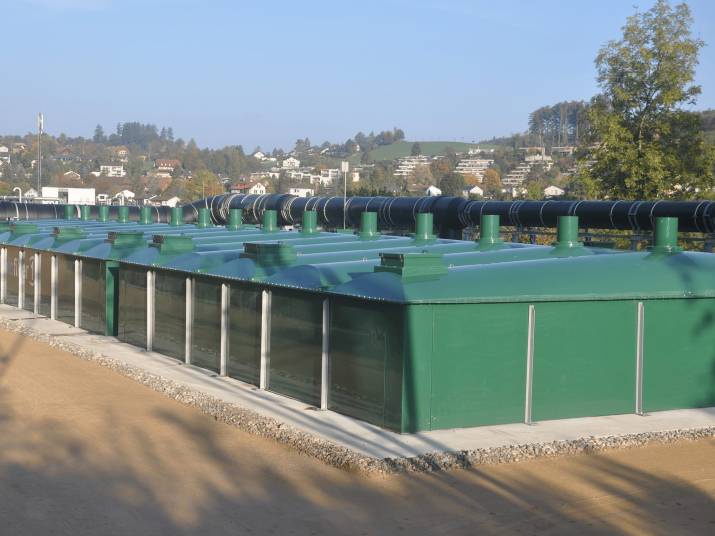
Bern waste water treatment plant / Switzerland
At the WWTP in Bern, 35,500 m³/h of odorous exhaust air is extracted from the waterway and cleaned. The extracted exhaust air is cleaned in a single-stage cross-flow scrubber that works according to the cross-flow principle and two parallel biofilters with a total area of 224 m².
60,000 Bm³/h of odorous exhaust air is extracted from the sludge treatment plant in Bern and cleaned in three parallel biofilters with a total area of 430 m². The pre-treatment and humidification of the exhaust air takes place in the pre-scrubber integrated in the biofilter.
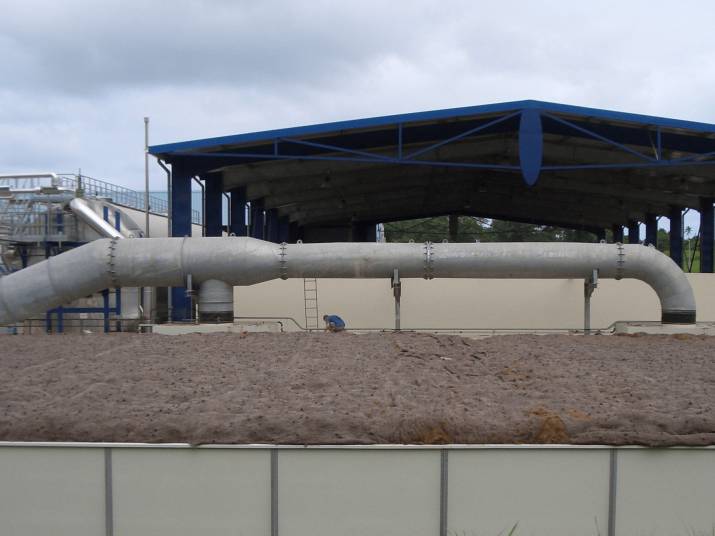
Composting Martinique
82,000 m³/h of exhaust air from a composting plant in Martinique are cleaned in a biofilter. It has a filter area of 660 m² and a pre-scrubber based on the cross-flow principle.
FAQ about the biofilter
The biofilter housing is made of GRP, but can also be manufactured in concrete at the customer’s request.
The temperature should be between 15 and 38°C.
Without chemical pre-treatment, the input values should not exceed 5 mg/m³.
As the bacteria first have to build up and multiply, this depends heavily on the type of exhaust air. The adaptation period can last from a few weeks to half a year.
The biofilter material is usually replaced after 3 – 5 years.
No. As the exhaust air is 100 % humid and flows slowly through the biofilter material from the bottom to the top, this humidity is sufficient.
Yes, the biofilter can be completely covered with a GRP tunnel roof.
With newly installed material, the pressure loss is approx. 150 Pascal. At the end of the service life of the biofilter material, this can rise to 500 Pa.