for the chemical industry
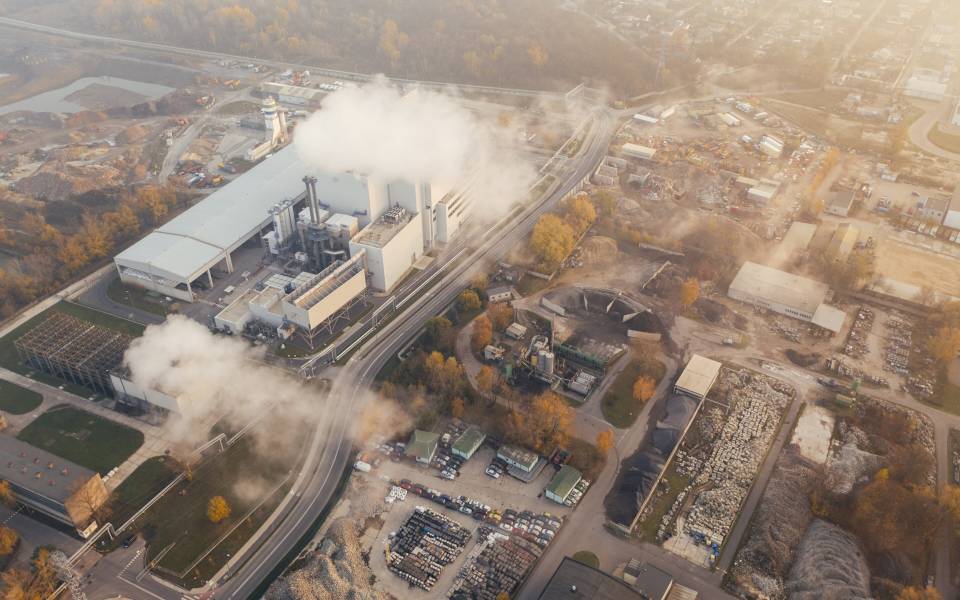
for the chemical industry
Challenges
of the chemical industry
As different as your products and processes are, as different are the emissions they produce. Organic and inorganic acids, ammonia or complex pollutant mixtures must be safely removed from the exhaust air before being discharged into the atmosphere. Production-specific features, such as strongly fluctuating exhaust air volumes, changing pollutant concentrations or temperature windows, must be taken into account when selecting and dimensioning the exhaust air purification system.
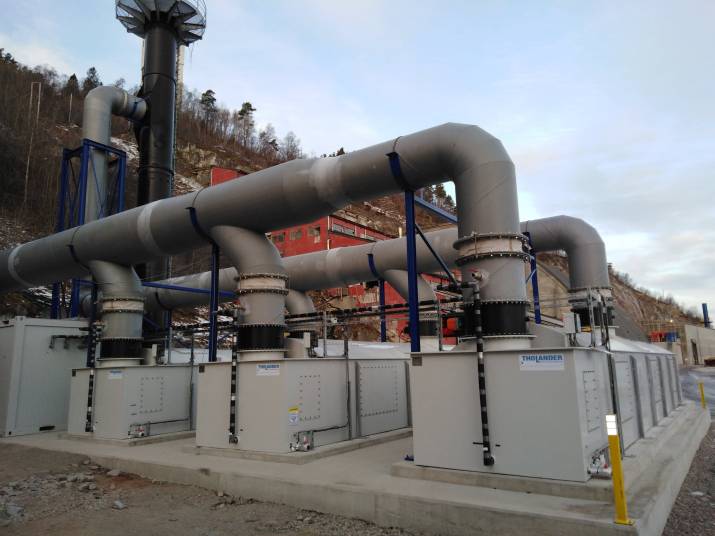
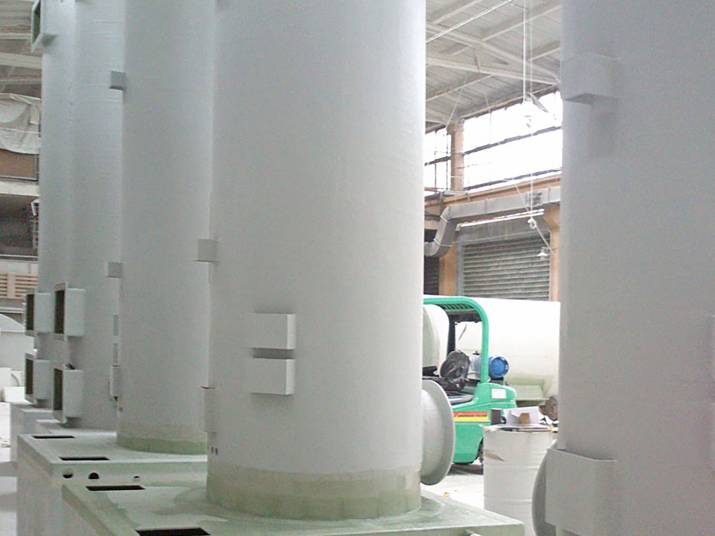
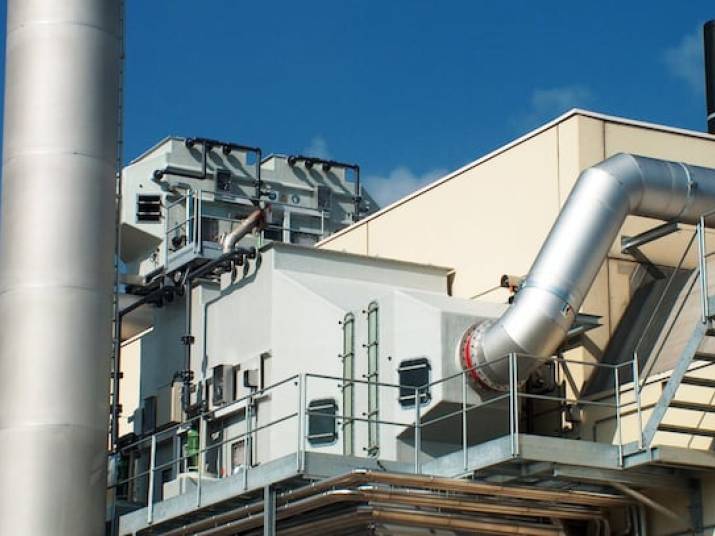
Our solution
Depending on the exhaust air purification task, we offer you solutions from a single source based on our core competences. Depending on the pollutants, single or multi-stage packed-bed scrubbers in counterflow or cross-flow design, multi-venturi scrubbers, biofilters or activated carbon filters are used. In many applications, combinations of several processes are useful in order to fully utilise the respective strengths of the processes.
To quote Albert Einstein, the description of the task is 95% of the solution. It is therefore important to us to know your needs, emissions and goals as precisely as possible. We take the necessary time to do this. In a joint analysis, we will clarify the relevant issues and, if necessary, supplement them with on-site measurements. Based on our many years of experience in a wide range of industries, we can then develop customised solutions, discuss alternatives and ultimately present a solution that suits your exhaust air purification task.
Our processes in project management, production, service and assembly are certified. We select our suppliers carefully and focus on long-term partnerships. This enables us to guarantee the reliable and high quality of our system as well as the purchased parts and external services.
We provide you with expert advice and support throughout the entire project. From checking the functionality and assessing the overall system to regular maintenance – we ensure that your system always runs optimally.
The materials we use are adapted to the respective requirements in terms of corrosion and resistance. For example, we usually manufacture our housings from glass fibre reinforced plastics (GRP). Appropriate resins, additives and manufacturing techniques guarantee high resistance and durability.
The optimisation of production processes, the use of energy-efficient machines and systems and the implementation of intelligent control and monitoring systems can significantly reduce energy costs. The economical use of resources such as water, raw materials and packaging materials also helps to conserve resources and reduce environmental pollution. We attach great importance to this, both in our own production and in the planning of your systems.
Concepts implemented worldwide
in the chemical industry
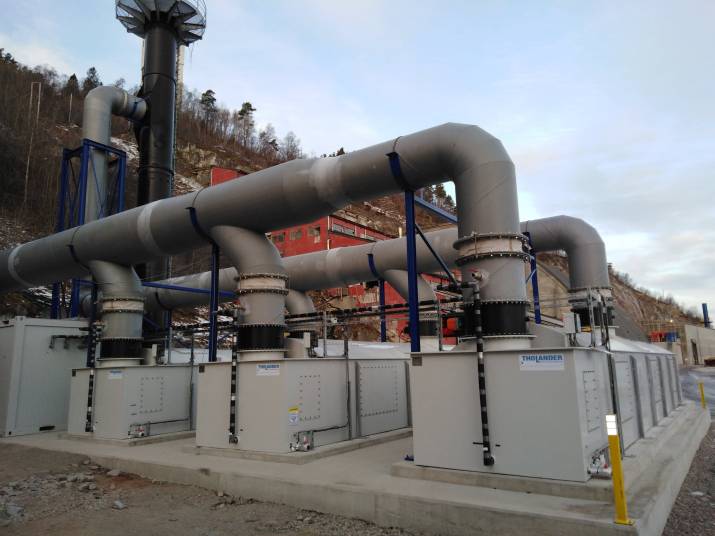
Phosphine (PH3) separation in Norway
In addition to ammonia, the vapours produced during the processing of aluminium also contain the extremely toxic phosphine. After separation of the ammonia in an acid-operated packed-bed scrubber, the phosphine is adsorbed in a multi-line activated carbon filter up to the detection limit. An online measurement permanently monitors the functionality of the system.
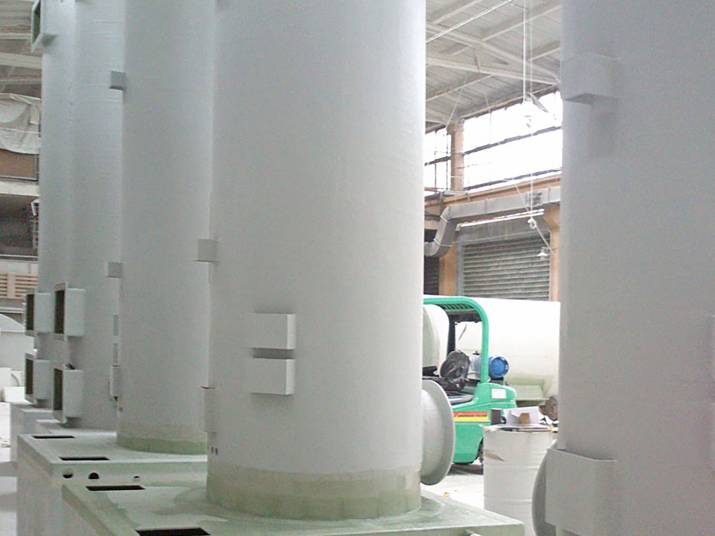
Limestone dissolving plant in Egypt
In the limestone dissolution plant for the extraction of technical CO2 in Egypt, the hydrochloric acid vapours and aerosols produced are separated in two packed scrubbers. The hydrochloric acid produced here is concentrated in the first column to such an extent that it can be fed back into the process. The second scrubbing stage ensures compliance with the strict standards for keeping the air clean.