Activated Carbon Filter
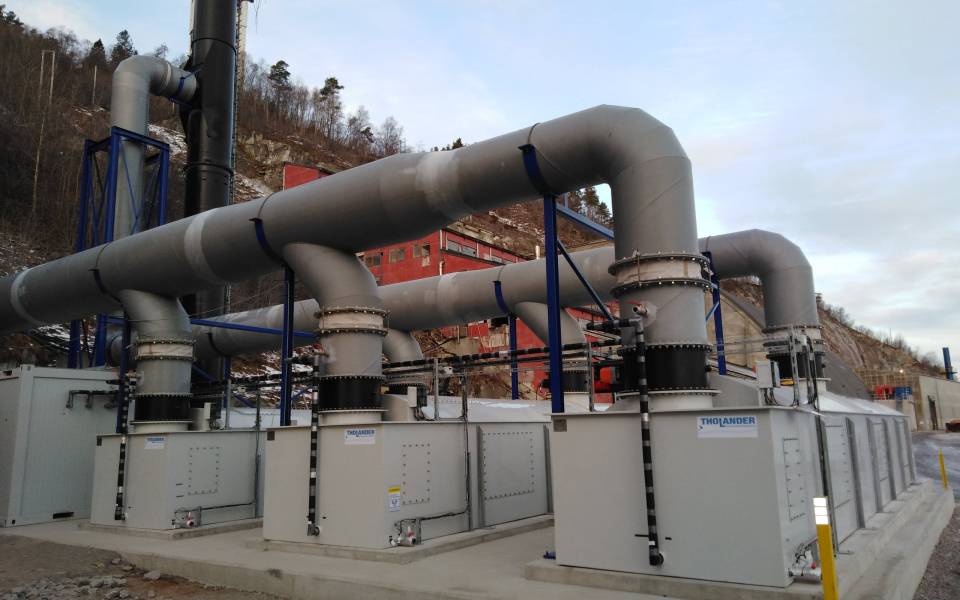
Activated Carbon Filter
Proven system rethought
Discover the highly efficient solution for odour removal: Activated carbon filters. This technology uses the unique adsorptive properties of activated carbon to remove unwanted odours from the air. Due to its large inner surface area, the activated carbon effectively attracts odour molecules and binds them safely without the use of chemicals. Ideal for a wide range of applications, from wastewater treatment to food production, our activated carbon filter system offers a reliable solution that meets the highest standards in air quality. Rely on proven technology for clean and fresh air in any environment – with our activated carbon filters, unpleasant odours are no longer a problem.
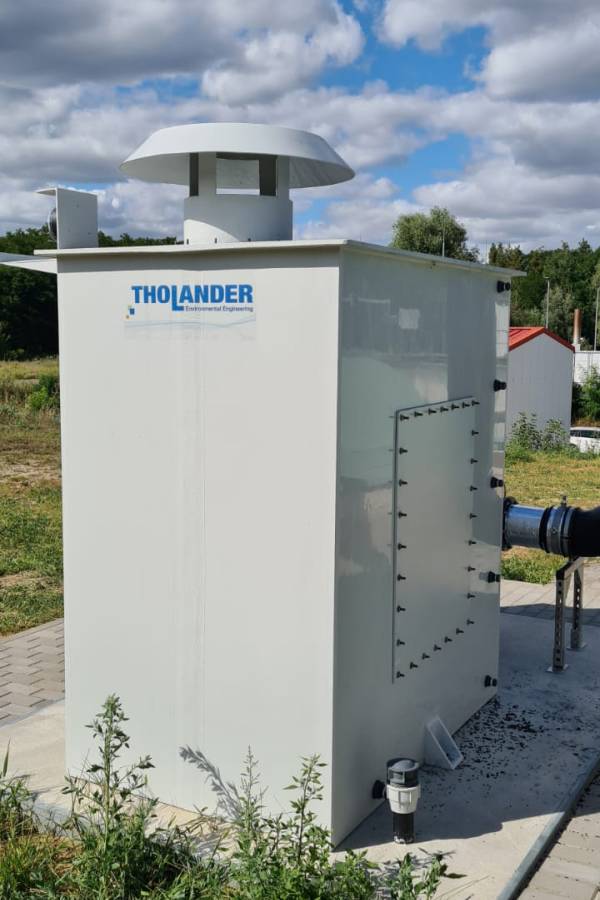
Benefit from an
activated carbon filter
- Universal applicability
- Multiple in-situ regeneration possible
- No additional energy consumption
- Low pressure loss due to hard and abrasion-resistant activated carbon
- humidity levels Up to 98% humidity
- Particularly suitable for humid air from sewers and sewage treatment plants
- Manholes provided for filling or replacement
- Sampling nozzle for measuring the load of the activated carbon
- System components made of corrosion and chemical-resistant materials
- Active references of all sizes
- Worldwide delivery
Conception
Our activated carbon filter is constructed in layers. The bottom layer consists of a cavity into which the air is blown in with the fan. Above the cavity is a grating covered with a close-meshed wire mesh. The activated carbon bed is located on the grating.
In the filter, the air moves slowly through the activated carbon bed, adsorbing the foul-smelling organic compounds. After treatment, the air is discharged into the atmosphere via the clean air nozzle.
Activated carbons must be changed or regenerated regularly, as they become loaded with adsorbed compounds during use and their capacity decreases over time. The saturation of the activated carbon is proven by test nozzles and our reliable, portable or stationary measuring devices. This allows the operator to measure the concentration of e.g. hydrogen sulphide under, inside or after the activated carbon bed. In this way, the exchange or regeneration time of the activated carbon can be estimated.
Despite the need for regular replacement or regeneration, the technology is very effective and environmentally friendly as it requires no chemicals and generally retains the adsorbed compounds safely in the activated carbon.
Applications
- Pumping station
- Waste water treatment plant
- Pharmaceutical production
- MBT
- Solvent degradation
- Composting plant
Projects implemented worldwide
with an Activated Carbon Filter
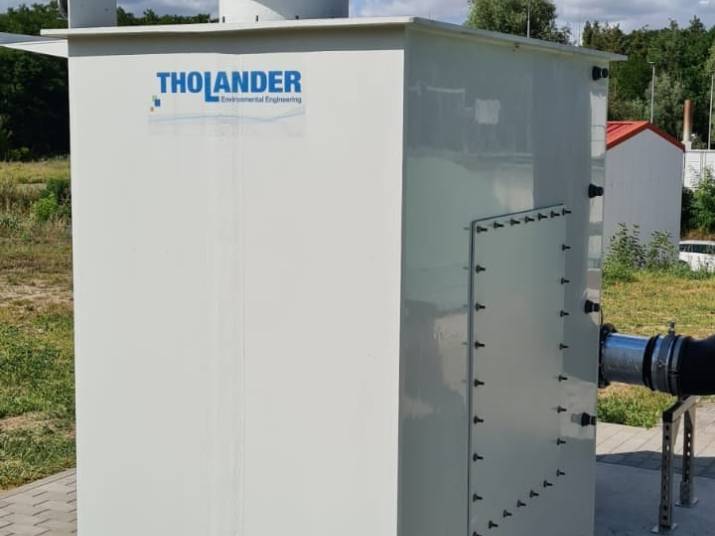
Wastewater treatment plant Zossen/Germany
At the Zossen sewage treatment plant, 4,200 m³/h of H2S-contaminated exhaust air is extracted from the enclosed screening hall and cleaned. The exhaust air is drawn in with a fan and cleaned in an activated carbon filter. This is installed outdoor.
In a second plant, the exhaust air from a covered pre-treatment system is treated. Here, 1,400 m³/h of H2S-contaminated exhaust air is cleaned in an activated carbon filter.
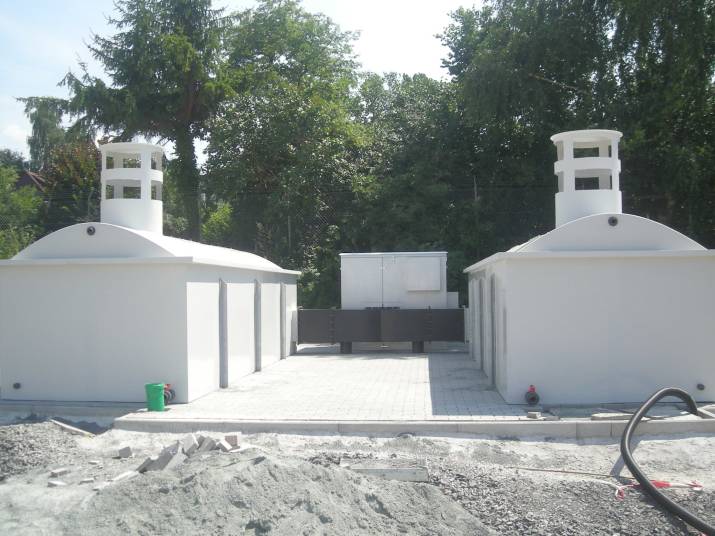
Rainwater overflow basin Ober-Ramstadt/Germany
30,000 m³/h of odorous exhaust air is extracted and purified from a rainwater overflow and rainwater retention basin in Ober-Ramstadt. The activated carbon containers are filled with a water-regenerable activated carbon that has been specially developed for the degradation of H2S and other odorous substances from sewage treatment plants and sewers.
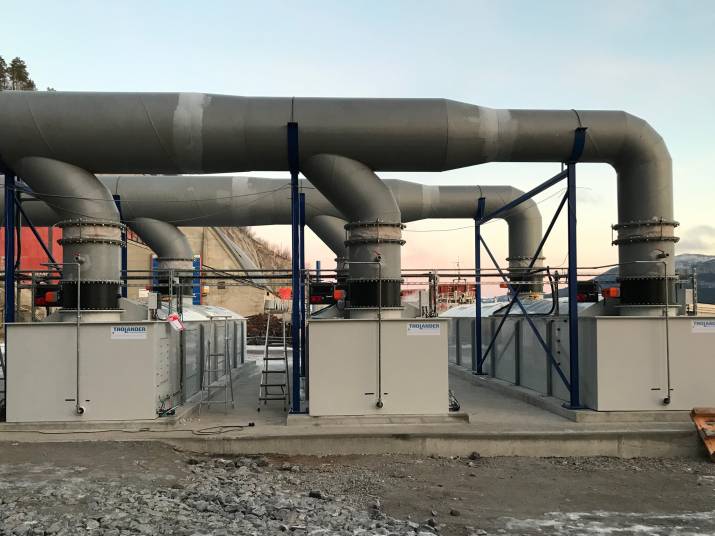
Process exhaust air Raudsand/Norway
The exhaust air to be treated comes from a slag containing alumina salt. The activated carbon filter is designed to remove the remaining phosphine. A maximum of 60,000 m³/h of process exhaust air can be cleaned.
FAQ about the Activated Carbon Filter
No, the filter is open at the top and therefore not gas-tight.
The activated carbon needs 30-40% relative humidity for the reactions.
There are different activated carbons with different requirements. The majority of carbons have a maximum moisture content of approx. 70%. After that, the separation performance decreases sharply. However, there are also carbons that can work with up to 95% humidity.